Special
Layout Tips & Tricks - from developers for developers
In this section, you will find assistance and suggestions on how to design your printed circuit board to meet production requirements and avoid later increased handling and production costs during assembly production.
![[Translate to Englisch:] [Translate to Englisch:]](/fileadmin/_processed_/f/c/csm_Tipps_und_Tricks_Website1900x1267-01_de6ceb914d.jpg)
Layout Tipps & Tricks
Bonding SMT components
There are three restrictions for wave soldering of previously glued SMT components:
- Components with a length ≤ 1.2 mm (e.g. component size 0402) cannot be soldered to the wave. They can no longer be glued with sufficient safety. Size 0603 should be avoided in wave soldering technology, as the process reliability is lower than with larger sizes
- Components with a height > 2.5 mm can easily be flushed away by the pressure of the wave or, if the height is even greater, they can get stuck on stationary parts of the wave soldering system. The heat sensitivity of film capacitors must be taken into account.
- Ceramic capacitors above size 0805 should not be soldered to the wave due to thermal stress.
It is common practice to bond SMT components in a separate process step and solder them together with the THT components on the solder side above the solder wave. Care must be taken to ensure that the SMT components are aligned in the direction of the shaft, as otherwise solder shadows will lead to unsoldered components. (see illustration)
In addition, attention must be paid to possible short circuits with transverse ICs. ICs with a 0.8 mm pitch can still be soldered without solder bridges if the layout is suitable for the wave (solder catchers present and correctly positioned components). Solder catchers should be twice as long as the pad and rounded or pointed at the end. (see SO14 in the illustration)
If no or rectangular solder catchers are used, solder sloshing back can lead to solder beads or short circuits between the pins.
With the 0.8 mm grid, there is a free distance of approx. 0.4 mm between the neighboring pads. The practical achievability of the wave soldering minimum depends, among other things, on the local topology of the assembly and the associated flow conditions on the assembly. Tests should be carried out before starting series production. The practical soldering limit for a solder bridge-free wave soldering result with standard systems is a uniform minimum distance of around 0.4 mm to 0.5 mm.
Climate tests
Electronic assemblies can be subjected to climate tests to simulate environmental influences. This is particularly important for products that are used worldwide under a wide range of environmental conditions.
In a climate test, the proper functioning of an assembly is tested in a climate chamber with changing temperature and humidity values. These tests can be carried out on different occasions:
- During the development of an assembly to stabilize the design under different environmental conditions.
- Sampling tests for production batches
- Climatic test of each individual assembly produced after production
- Pre-aging of electronic assemblies
NOTE: Climate chambers only have a limited volume to accommodate electronic assemblies. Please clarify the possible dimensions of the PCBs with your EMS service provider in good time.
X-ray analyses for quality assurance
Quality assurance has numerous options for carrying out random tests on prototypes and series products.
One option that Ginzinger electronic systems also uses is X-ray analysis. Electronic assemblies with BGAs and LGAs can thus be analyzed with regard to soldering quality.
Potential weak points are detected immediately thanks to high-quality X-ray images and computer tomography. Whether component positioning, any voids in the solder joint or short circuits - images can be taken using an X-ray detector with a 6.7 megapixel camera and 0.1 µm resolution.
Tomosyntheses or complete µCT images are created in a short time. The 3D inspection also enables detailed sectional and layered images of electronic assemblies and components. Specific layers, fractures or cracks can be viewed on multilayer PCBs. Encapsulated components can also be inspected, as can relevant interfaces (fill level and other quality features).
Ginzinger electronic systems also offers X-ray analysis as a service for industries outside of electronics.
Printed circuit board holes
Holes in printed circuit boards can have the following tasks:
- Through-holes (vias) are electrical connections between different layers.
- Through-holes for soldering THT or THR components.
- Mounting holes
- Holes for feedthroughs
The diameters of the drill holes should be standardized. Thus, less time is needed for a tool change. I.e. only one diameter should be selected for all vias if possible. Mounting holes should also have a uniform diameter.
Mounting holes
Printed circuit boards can be fixed in a housing by conductive or insulating fixing points. To avoid damage, interruptions or short circuits, clearances and tolerances should be considered. If fixing points are used as electrical connections, care should be taken to ensure that the connection between the conductive track and the contact surface is outside the screw head or washer to prevent the connection being severed when the screw is screwed in.
Restricted zones for fastening holes
Restricted zones should be defined around fastening holes into which no components, connections or pads may extend.
Fiducials & Zero Marking
Fiducials are used on electrical circuit boards as optical reference points for automated production processes. The fiducials are detected optically. Depending on the requirements, several fiducials are placed on the surface of the PCB to meet the high accuracy requirements. For good detectability, a fiducial mark should have the following characteristics:
- Copper disc diameter of about one millimeter
- ring with inner diameter of 2 millimeters
- Solder resist release with a diameter of 4 millimeters
Three fiducial marks should be present on each side of the PCB to be assembled. The marks shall be placed diagonally at maximum distance on the PCB side. The fiducial marks must be positioned in such a way that the automatic differentiation between TOP and BOT side is possible.
Component weight
Particularly in the case of printed circuit boards with SMT components on both sides, attention must be paid to the weight of the components in order to avoid costs for additional process steps. The decisive factor is the component weight per component connection area. Very heavy components that exceed the component weight limit cannot be processed in the SMT process during the first soldering step. There is a risk that they will drop overhead during the second soldering process. All heavy components should be placed uniformly on only one side of the PCB (TOP or BOT).
Criteria for identifying heavy SMT components are:
- Component height > 4 mm
- RM > 1.27 mm
- Body volume > 50 mm3/connection
- Strongly asymmetric pins or packages
An approximation is also provided by the formula: max. component weight < L*b*0.05*n
L = length of component connection (minimum value)
b = width of component connection (minimum value)
0.05 = component weight 0.05 g/mm2
n = number of connections
Note: If the limit weight cannot be maintained, heavy components can be glued before the soldering process. An adhesive dispenser is used for this purpose. For further information please contact the Ginzinger electronic systems team.
Paste printing
Statistically, 64% of the production defects in an SMT production can be traced back to faulty paste printing. Special attention must therefore be paid to this area. Solder paste printing must be fully automated to prevent errors caused by manual intervention. High printing speed reduces machine times and costs.
Paste data should be stored by the PCB designer in a separate layer in the Gerber file. The stencil production data is generated on these. Based on further information and experience, the EMS service provider can provide suitable enlargements or reductions of individual openings in the stencil.
Squeegees made of stainless steel or plastic wipe the solder paste over the print stencil. The solder paste is thereby pressed through the stencil openings and remains at the desired locations on the PCB. Excess paste is scraped off the stencil surface by means of a squeegee.
In modern SMT production lines, a 3D solder paste inspection (SPI) system measures the printed volume of solder paste over the entire PCB surface after paste printing. Faulty printing can therefore be corrected immediately in this process step.
Placement printing
The placement print helps with measuring and troubleshooting on electronic assemblies. The correct alignment of components can also be easily checked by marking them using placement printing (pin 1). However, due to the ever increasing miniaturization, it should be considered whether such placement printing is still useful. All free copper areas (pads, vias) are left blank by the PCB manufacturer. Thus, poorly positioned prints quickly become illegible.
The extent of the placement print should be minimal, precisely defined and one should consider whether it is really necessary. It should be noted that the paste stencil cannot lie flat on the PCB during placement printing and there is a risk that no clean solder deposit can be printed. Under components, placement printing should be dispensed with entirely.
Test and testability of assemblies
Measures for the final tests and commissioning of the electronic printed circuit boards after the production process should be considered in the design from the beginning.
- Provide trap holes for the PCB (asymmetrical, typ. 3.2 mm, not plated through and not tinned.) Consider keep-out zones!
- Test points in each electrical node; vias can be used as test points provided they have> 0.8mm pad diameter and are not covered.
- Distance of the test points to each other and to the PCB edge > =2.54 mm; In exceptional cases and after consultation, the distance can be reduced to up to 1.27 mm. This leads to higher costs in the test equipment.
- Test points should be placed evenly on the PCB in order to distribute the forces by contact needles in a balanced way.
- For supply voltage networks, several test points should be placed. These should be distributed on the PCB or positioned at the beginning and end of the trace.
- Test points should preferably be placed only on the component-free side or the side with the lowest components.
- In the case of metrologically critical components (low-resistance shunts), a four-wire measurement should be provided.
- Components which have an enable input should be switched to "high" or "low" in the design via a pullup/pulldown. This gives the possibility to deactivate them during the test.
- SMD and THR solder joints must not be used as test points, as they may be contaminated by flux residues. Contacting is then not possible.
- A test point diameter of 1mm, but min. 0.8 mm is recommended.
Solder / Solder
The solder (or brazing tin) is used to join metals by soldering. The solder consists of an alloy of different metals. The melting point of the solder is lower than that of the workpieces to be joined. In the past, lead was contained in many solders. Since 2007, these solders may only be used in exceptional cases in the EU in accordance with the RoHS Directive.
The solder for reflow soldering is applied in paste form. The paste consists of small tin balls and flux. The solder paste is available in different grain sizes. If electronic assemblies are subjected to different soldering processes (reflow, wave and manual soldering), the solder used should be matched so that no undesirable metallurgical effects occur.
General selection criteria for electronic components
Electronic components are selected primarily on the basis of functional requirements. In order to keep total cost of ownership (TCO) low over the complete life cycle of an assembly, the following criteria should be considered in the selection process:
- Long-term unit cost
What is the unit price of the component and what scale prices can be achieved over a longer period? - Availability
It is worth consulting suitable databases in advance to check the long-term availability of a component. - Second Source
Are components available from several sources or can components with several sources be preferred? This ensures long-term availability from different sources. - Common housing variants
Is a component really only available in a certain package variant from one source? Can another housing variant be used that can be obtained from multiple sources? - Preferred components
Are there preferred components in the company or at your EMS service provider that can be used? Can a price and availability advantage be achieved from this? - Component variants
Can the number of component variants be reduced? For example, can capacitors with identical capacitance also have a uniform dielectric strength?
NOTE: Ginzinger electronic systems offers services for the life-cycle check of your assembly to ensure a long-term, economical production of the product.
Cost-conscious development
The production costs of an electronic assembly are determined during development. Many important decisions are made here.
- Is one-sided assembly possible?
Especially if only a few components are to be assembled on the second side of the PCB, production costs can be saved by shifting to only one side. - Are many different components of the circuit used or can some components and values be standardized?
Reducing the number and variance of components saves setup costs in production. - Can the packaging of the components, such as rolls, bars or trays, which is optimally suited for later processing already be influenced in the development phase during component selection?
Automatable packages with a higher number of components save storage and production costs. - Is it possible to use a cheaper chip technology?
LVC standard logic is cheaper than HC, for example. - Can connectors or relays in THR technology be used?
These can be soldered more cost-effectively and fully automatically in the reflow process. An additionally required THT process is saved. - Is a higher product class and thus more expensive processes and materials really necessary?
Standards and guidelines are often over-interpreted or additional safety features are built in. These no longer significantly reduce the risk of a system, but greatly increase the costs. - Are multifunctional problem solutions possible?
- Can a housing also be used as a heat sink, for example?
- Can costly special tools for processing and production be avoided?
Possibly, after minor adjustments, the production step can also be carried out with inexpensive standard tools. - Are all components also available in the long term?
A timely life cycle check with a suitable database prevents expensive revisions in advance. - Which components are subject to a particular risk?
Large ceramic capacitors, for example, are sensitive and can break easily in the production process. - Have all possible component shapes been considered?
Smaller shapes of a component can often be better automated and processed at lower cost.
However, component shapes and pin spacing that are too small can also lead to increased costs. Coordinate in good time with your EMS service provider which build shape will give you the cost optimum from material price and production costs.
Tips and tricks from 30 years of experience in electronics production can be found in our EMS Design Guide. Our practical little helper is now available in a new and completely revised 4th edition. For free pre-order:
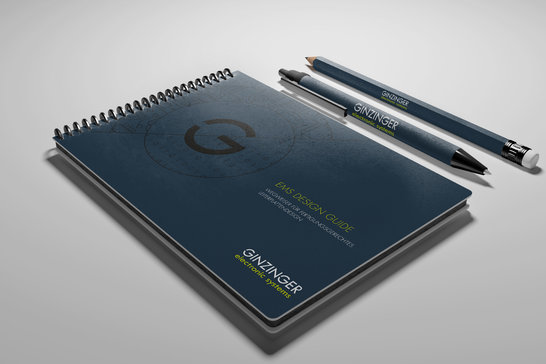