Aktuelles
Ultraschallschweißen bei Ginzinger
Mit der neuen Ultraschallschweißanlage können kundenspezifische Kunststoffgehäuse für elektronische Baugruppen in kurzer Zeit dicht verschweißt werden.
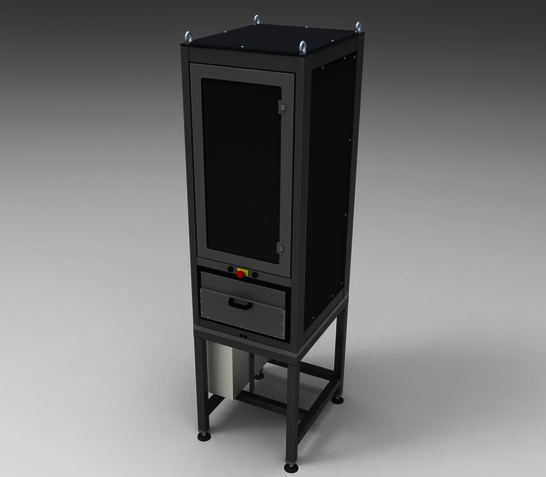
Der Ginzinger Maschinenpark wurde wieder um ein technisches Schmankerl erweitert: Mit der neuen Ultraschallschweißanlage können kundenspezifische Kunststoffgehäuse für elektronische Baugruppen in kurzer Zeit dicht verschweißt werden. Der Bedarf für das neue Verfahren ist durch Kundenprojekte entstanden.
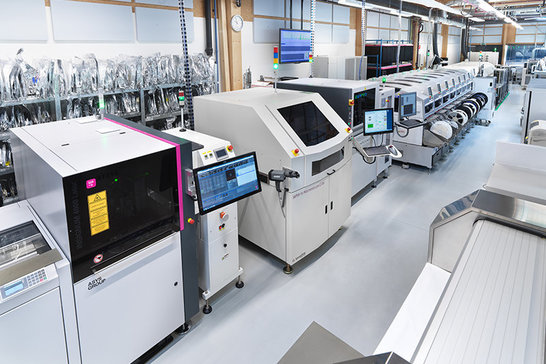
In einem konkreten Projekt wird eine Telematik-Baugruppe in ein dicht verschweißtes Gehäuse montiert. Diese müssen anspruchsvollen Umweltbedingungen im Einsatz an Kraftfahrzeugen und Frachtcontainern genügen. Dazu bedarf es eines dichten, robusten, aber leichten Kunststoffgehäuses, das Temperaturschwankungen, Sonneneinstrahlung und Vibrationen verlässlich standhalten muss, um die darin verbaute Elektronik zu schützen. Die elektronischen Baugruppen werden nach erfolgter Bestückung in Kunststoffteile eingesetzt und versiegelt. Nach intensiver Recherche der Ginzinger-Experten, welche Technologie für diese Anforderung am besten geeignet ist, fiel die Entscheidung gemeinsam mit einem Kunden auf das Verfahren des Ultraschallschweißens.
Was ist Ultraschallschweißen?
Ultraschallschweißen ist im Grundprinzip ein festes Verpressen zweier Gehäuseteile. Diese Verpressung erfolgt unter gleichzeitigem Einbringen von Ultraschallwellen. Der Ultraschall verursacht Mikrobewegungen, dadurch entsteht Reibung und Wärme. Die Wärme lässt das Material schmelzen, wodurch sich die Kunststoffteile verbinden.
Bei den Gehäuseteilen kommt ein spezieller Kunststoff zum Einsatz. Dieser ist faserverstärkt und kommt im Automobilbereich in der Serienproduktion für Komponenten im Außenbereich zum Einsatz. Nach Vorselektion diverser Hersteller für Ultraschallschweißgeräte bei Ginzinger electronic systems wurden im Frühjahr und Sommer 2022 Gespräche geführt und Angebote eingeholt. Schließlich fiel die Wahl auf den holländischen Hersteller AESON. Im Dezember 2022 wurde das 400 Kilogramm schwere Gerät aufgestellt und in Betrieb genommen. Stefan Schlägl über die Implementierung des neuen Gerätes in der Produktion:
„Die Etablierung dieses komplett neuen Prozesses bei uns in der Produktion ist durchaus komplex. Bis der Ablauf reibungslos funktioniert, ist sehr viel Vorbereitung und Aufbau von Knowhow notwendig. Der Schweißvorgang selbst ist dann aber sehr schnell und effektiv, denn die Schweißung selbst dauert nur wenige Sekunden pro Gehäuse.“
Einfach & schnell
Das ist im Vergleich zum Einsetzen von Dichtungen oder dem Prozess des Klebens, bei dem viele Faktoren wie Material, Form, Klebemenge, Kontaktierung, Ablaufdatum, Temperatur, Trocknungsdauer, hinzukommen einfach und schnell. Das Ultraschallschweißgerät muss produktspezifisch ausgerüstet werden.
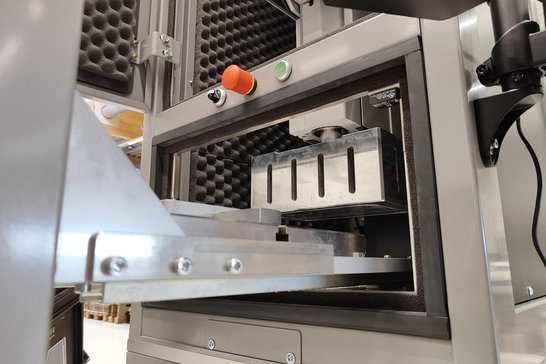
„Das zu schweißende Gehäuse unterliegt dem Kundendesign. Die produktspezifischen Werkzeuge für ein Kundenprojekt, wie die Einspannvorrichtung, werden maßgeschneidert angefertigt und gehören dem Kunden. Die benötigten Geometrien für die benötigte Schweißnaht werden ganz genau mit dem Kunden abgestimmt und ausgearbeitet“,
Alexander ist der Verantwortliche für das Schweißgerät bei Ginzinger und war auch bereits bei Einschulung und der technischen Abnahme in Holland mit dabei. Er freut sich auf den intensiven Einsatz im Haus und ist zuversichtlich künftig viele Kundenprojekte damit betreuen zu können, bei dem der Ultraschall-Schweißprozess einen klaren Vorteil bringt.